SERVICES
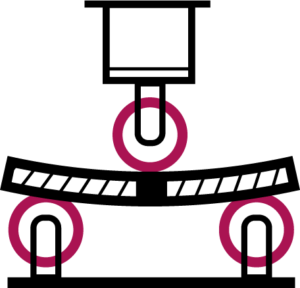
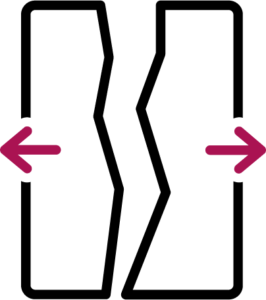
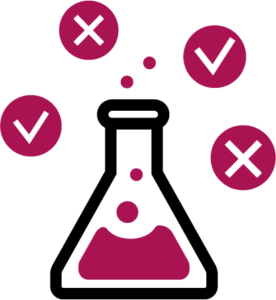
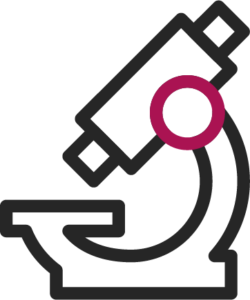
Accredited test methods of destructive tests on welds for welders (EN ISO 9606) and weld procedures (EN ISO 15614) certification:
- Bend test EN ISO 5173
- Fracture test EN ISO 9017
- Transverse tensile test EN ISO 4136
- Longitudinal tensile test EN ISO 5178
- Impact test EN ISO 9016
- Hardness test EN ISO 9015-1
- Microhardness test EN ISO 9015-2
- Micro- and macrostructure analysis EN ISO 17639
- Percentage of ferrite EN ISO 17639
Additionally we offer different accredited test methods of destructive tests on resistance spot welds and railway applications (EN 14587-2, EN 14730-1).
Accredited test methods of destructive tests on welds for welders (EN ISO 9606) and weld procedures (EN ISO 15614) certification:
- Bend test EN ISO 5173
- Fracture test EN ISO 9017
- Transverse tensile test EN ISO 4136
- Longitudinal tensile test EN ISO 5178
- Impact test EN ISO 9016
- Hardness test EN ISO 9015-1
- Microhardness test EN ISO 9015-2
- Micro- and macrostructure analysis EN ISO 17639
- Percentage of ferrite EN ISO 17639
Additionally we offer different accredited test methods of destructive tests on resistance spot welds and railway applications (EN 14587-2, EN 14730-1).
Mechanical destructive test methods:
- Metallic materials tensile test at room temperature EN ISO 6892-1
- Metallic materials tensile test at elvated temperature EN ISO 6892-2
- Plastics and polymer composite materjals tensile test EN ISO 527-1… 4
- Metallic materials Charpy pendulum impact test EN ISO 148-1
- Metallic materials bend test EN ISO 7438
- Plastic materials bend test EN ISO 178
- Glass bend test EN ISO 572-1
- Products and component testing EN ISO 898, EN ISO 3506, EN ISO 15630, EN ISO 13674-1
Mechanical destructive tests are carried out mainly for materials and products conformity to requirements or standards and also during expertise for their actual mechanical properties determination.
- Destructive test load between 0.1 kN … 250 kN and temperature -80°C …+ 650°C.
- Slow (quasi-static) and/or cyclic loading (fatigue test).
- Products: fasteners, concrete reinforcing steel, railway rails.
- The most typical properties to be determined are tensile strength, yield strength, elongation at break.
- It is also possible to measure the deformations in 3D using cameras and the Digital Image Correlation – DIC method.
NB! All specimens are prepared according to standards requirements therefore it is essential to consent samples dimensions before testing!
Mechanical destructive test methods:
- Metallic materials tensile test at room temperature EN ISO 6892-1
- Metallic materials tensile test at elvated temperature EN ISO 6892-2
- Plastics and polymer composite materjals tensile test EN ISO 527-1… 4
- Metallic materials Charpy pendulum impact test EN ISO 148-1
- Metallic materials bend test EN ISO 7438
- Plastic materials bend test EN ISO 178
- Glass bend test EN ISO 572-1
- Products and component testing EN ISO 898, EN ISO 3506, EN ISO 15630, EN ISO 13674-1
Additionally we offer different customized non-standard tests, for more information please contact us directly or send your test request with order form!
Mechanical destructive tests are carried out mainly for materials and products conformity to requirements or standards and also during expertise for their actual mechanical properties determination.
- Destructive test load between 0.1 kN … 250 kN and temperature -80°C …+ 650°C.
- Slow (quasi-static) and/or cyclic loading (fatigue test).
- Products: fasteners, concrete reinforcing steel, railway rails.
- The most typical properties to be determined are tensile strength, yield strength, elongation at break.
- It is also possible to measure the deformations in 3D using cameras and the Digital Image Correlation – DIC method.
NB! All specimens are prepared according to standards requirements therefore it is essential to consent samples dimensions before testing!
Methods for chemical composition analysis:
- Spectral analysis (Atomic Emission Spectroscopy – AES)
- SEM-EDS – Scanning Electron Microscopy with Energy Dispersive Spectroscopy
Chemical composition is analysed mainly during conformity evalution to determine metals and their alloys actual chemical composition more precisely their chemical elements concentration.
Main Fe-based alloys (steel, cast iron), Cu-based alloys (bronze, brass etc.) and Al-based alloys chemical composition is determined usually with AES method. For smaller specimens it is possible to use induction melting device.
SEM-EDS method is used mostly for material microstructure, coatings or smaller specimens.
Methods for chemical composition analysis:
- Spectral analysis (Atomic Emission Spectroscopy – AES)
- SEM-EDS – Scanning Electron Microscopy with Energy Dispersive Spectroscopy
Chemical composition is analysed mainly during conformity evalution to determine metals and their alloys actual chemical composition more precisely their chemical elements concentration.
Main Fe-based alloys (steel, cast iron), Cu-based alloys (bronze, brass etc.) and Al-based alloys chemical composition is determined usually with AES method. For smaller specimens it is possible to use induction melting device.
SEM-EDS method is used mostly for material microstructure, coatings or smaller specimens.
Microstructure analysis methods:
- Steel grain size EN-ISO 643
- Steel non-metallic inclusions ASTM E45
Macrostructure analysis tests:
- Fracture surface analysis
- Porosity
- Micro/macro cracks
- The purpose of structural analysis of metals and their alloys is to evaluate material conformity to requirements and to assess heat treatment quality. Metals and alloys cleanliness (different inclusions), grain size and microstructure are evaluated.
- The purpose of fracture surface analysis is to identify the nature of fracture – brittle or ductile and root cause of failure for example overload, corrosion etc.
Light optical microscope optical magnification is between 4,7x … 1000x. In case of need, using scanning electron microscopy (SEM) enables using higher magnifications (up to 20.000x).
For microstructure analysis, preparing a cross-section from examined sample is needed. For that, sampled material is encapsulated with mounting with a plastic shell which prepares the sample for the following metallographic grinding, polishing and etching steps. Both, hot and cold mounting are available (cross-section diameter 25 mm … 50 mm).
LOM and/or SEM methods are used for macrostructure and fracture surface analysis.
Microstructure analysis methods:
- Steel grain size EN-ISO 643
- Steel non-metallic inclusions ASTM E45
Macrostructure analysis tests:
- Fracture surface analysis
- Porosity
- Micro/macro cracks
- The purpose of structural analysis of metals and their alloys is to evaluate material conformity to requirements and to assess heat treatment quality. Metals and alloys cleanliness (different inclusions), grain size and microstructure are evaluated.
- The purpose of fracture surface analysis is to identify the nature of fracture – brittle or ductile and root cause of failure for example overload, corrosion etc.
Light optical microscope optical magnification is between 4,7x … 1000x. In case of need, using scanning electron microscopy (SEM) enables using higher magnifications (up to 20.000x).
For microstructure analysis, preparing a cross-section from examined sample is needed. For that, sampled material is encapsulated with mounting with a plastic shell which prepares the sample for the following metallographic grinding, polishing and etching steps. Both, hot and cold mounting are available (cross-section diameter 25 mm … 50 mm).
LOM and/or SEM methods are used for macrostructure and fracture surface analysis.
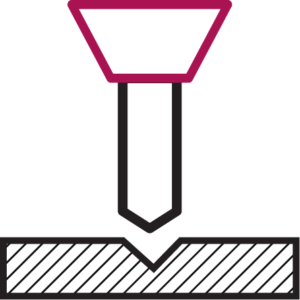
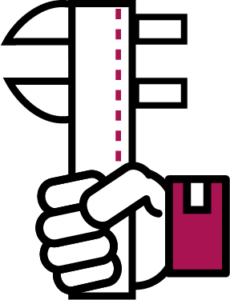
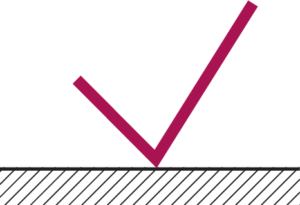
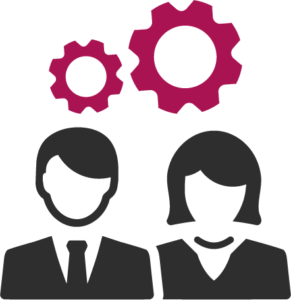
Hardness measurement methods:
- Brinell hardness EN-ISO 6506-1
- Vickers hardness EN-ISO 6507-1
- Rockwell hardness EN-ISO 6508-1
- Universal hardness (instrumented indentation test) EN-ISO 14577
Measuring material hardness enables to evaluate heat treatment conformity to requrements. For some materials, it is also possible to evaluate material tensile strenght through hardness measurement results.
Brinell hardness is mainly used for determine hardness of soft and medium hardness steels. Vickers hardness is used for welds and Rockwell hardness for tempered steel and aluminum alloys.
- Vickers scale HV 0,01 … HV 30.
- Brinell load 1 kgf … 3000 kgf, ball dimensions 1; 2,5; 5 and 10 mm.
- Rockwell scales HRA, HRB, HRC. Additional loads 15 kgf, 30 kgf and 45 kgf.
For all methods suitable sample shape, thickness and surface finish is required to carry out hardness measurement. For more information please contact us through order form.
Hardness measurement methods:
- Brinell hardness EN-ISO 6506-1
- Vickers hardness EN-ISO 6507-1
- Rockwell hardness EN-ISO 6508-1
- Universal hardness (instrumented indentation test) EN-ISO 14577
Measuring material hardness enables to evaluate heat treatment conformity to requrements. For some materials, it is also possible to evaluate material tensile strenght through hardness measurement results.
Brinell hardness is mainly used for determine hardness of soft and medium hardness steels. Vickers hardness is used for welds and Rockwell hardness for tempered steel and aluminum alloys.
- Vickers scale HV 0,01 … HV 30.
- Brinell load 1 kgf … 3000 kgf, ball dimensions 1; 2,5; 5 and 10 mm.
- Rockwell scales HRA, HRB, HRC. Additional loads 15 kgf, 30 kgf and 45 kgf.
For all methods suitable sample shape, thickness and surface finish is required to carry out hardness measurement. For more information please contact us through order form.
- Automated thermal cutting process capability control
EN 1090-2 - Average surface roughness and perpendicularity tolerance ISO 9013
Products and components geometrical and post-process workpieces control.
Examples of controlled products:
- wire strands;
- reinforcement and prestressed steels;
- thermal cut details.
- Automated thermal cutting process capability control
EN 1090-2 - Average surface roughness and perpendicularity tolerance ISO 9013
Products and components geometrical and post-process workpieces control.
Examples of controlled products:
- wire strands;
- reinforcement and prestressed steels;
- thermal cut details.
- Surface roughness measurement ISO 9013
Surface roughness measurements. Measurements are performed by contact profilometer, enabling main outputs as Ra, Rz, Rmax, Rp, Rv etc.
- Surface roughness measurement ISO 9013
Surface roughness measurements. Measurements are performed by contact profilometer, enabling main outputs as Ra, Rz, Rmax, Rp, Rv etc.
We offer a professional expertise work because we are used to the high demands of companies and have understanding of several production processes.
We also offer consultations and can assist in improving the production process and performing quality control of production. We have long-term experience of cooperation with industrial companies
Expertise is mostly used in finding out the reasons for the breakage or failure of parts or the processes. Expertise is not only performed to resolve disagreements between the parties, but also in situations where the manufacturer or the user of the product examines some product-related process or product characteristic:
- causes of breakage/wear of one particular part;
- fast machine part, etc., which occurred as a result of repair or reconstruction;
- breakage/wear; causes of scrap parts in production;
- the suitability/properties of the material used or applied.
When ordering expertise, the following circumstances must be taken into account:
- the expertise is performed on a specific material/detail brought by the customer;
- studies and opinions performed in expert examination must remain within the competence of the laboratory;
- it is not possible to answer all questions unambiguously.
For more informaton, please contact us thorugh order form!
We offer a professional expertise work because we are used to the high demands of companies and have understanding of several production processes.
We also offer consultations and can assist in improving the production process and performing quality control of production. We have long-term experience of cooperation with industrial companies.
Expertise is mostly used in finding out the reasons for the breakage or failure of parts or the processes. Expertise is not only performed to resolve disagreements between the parties, but also in situations where the manufacturer or the user of the product examines some product-related process or product characteristic:
- causes of breakage/wear of one particular part;
- fast machine part, etc., which occurred as a result of repair or reconstruction;
- breakage/wear; causes of scrap parts in production;
- the suitability/properties of the material used or applied.
When ordering expertise, the following circumstances must be taken into account:
- the expertise is performed on a specific material/detail brought by the customer;
- studies and opinions performed in expert examination must remain within the competence of the laboratory;
- it is not possible to answer all questions unambiguously.
For more informaton, please contact us thorugh order form!
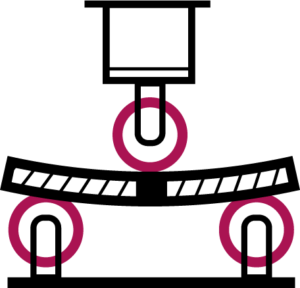
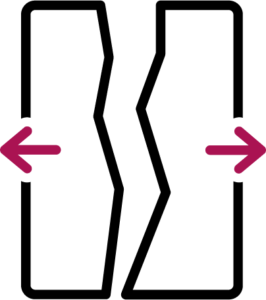
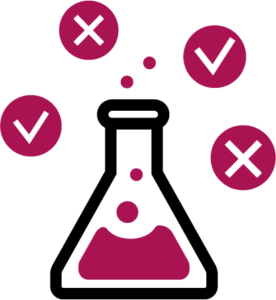
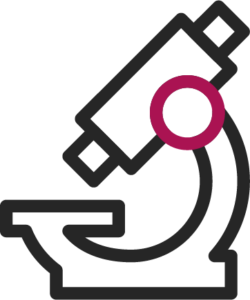
- Testing of welds
- Mechanical testing
- Determination of chemical composition of metals and alloys
- Structural analysis of metals and alloys
Accredited test methods of destructive tests on welds for welders (EN ISO 9606) and weld procedures (EN ISO 15614) certification:
- Bend test EN ISO 5173
- Fracture test EN ISO 9017
- Transverse tensile test EN ISO 4136
- Longitudinal tensile test EN ISO 5178
- Impact test EN ISO 9016
- Hardness test EN ISO 9015-1
- Microhardness test EN ISO 9015-2
- Micro- and macrostructure analysis EN ISO 17639
- Percentage of ferrite EN ISO 17639
Additionally we offer different accredited test methods of destructive tests on resistance spot welds and railway applications (EN 14587-2, EN 14730-1).
Accredited test methods of destructive tests on welds for welders (EN ISO 9606) and weld procedures (EN ISO 15614) certification:
- Bend test EN ISO 5173
- Fracture test EN ISO 9017
- Transverse tensile test EN ISO 4136
- Longitudinal tensile test EN ISO 5178
- Impact test EN ISO 9016
- Hardness test EN ISO 9015-1
- Microhardness test EN ISO 9015-2
- Micro- and macrostructure analysis EN ISO 17639
- Percentage of ferrite EN ISO 17639
Additionally we offer different accredited test methods of destructive tests on resistance spot welds and railway applications (EN 14587-2, EN 14730-1).
Mechanical destructive test methods:
- Metallic materials tensile test at room temperature EN ISO 6892-1
- Metallic materials tensile test at elvated temperature EN ISO 6892-2
- Plastics and polymer composite materjals tensile test EN ISO 527-1… 4
- Metallic materials Charpy pendulum impact test EN ISO 148-1
- Metallic materials bend test EN ISO 7438
- Plastic materials bend test EN ISO 178
- Glass bend test EN ISO 572-1
- Products and component testing EN ISO 898, EN ISO 3506, EN ISO 15630, EN ISO 13674-1
Mechanical destructive tests are carried out mainly for materials and products conformity to requirements or standards and also during expertise for their actual mechanical properties determination.
- Destructive test load between 0.1 kN … 250 kN and temperature -80°C …+ 650°C.
- Slow (quasi-static) and/or cyclic loading (fatigue test).
- Products: fasteners, concrete reinforcing steel, railway rails.
- The most typical properties to be determined are tensile strength, yield strength, elongation at break.
- It is also possible to measure the deformations in 3D using cameras and the Digital Image Correlation – DIC method.
NB! All specimens are prepared according to standards requirements therefore it is essential to consent samples dimensions before testing!
Mechanical destructive test methods:
- Metallic materials tensile test at room temperature EN ISO 6892-1
- Metallic materials tensile test at elvated temperature EN ISO 6892-2
- Plastics and polymer composite materjals tensile test EN ISO 527-1… 4
- Metallic materials Charpy pendulum impact test EN ISO 148-1
- Metallic materials bend test EN ISO 7438
- Plastic materials bend test EN ISO 178
- Glass bend test EN ISO 572-1
- Products and component testing EN ISO 898, EN ISO 3506, EN ISO 15630, EN ISO 13674-1
Additionally we offer different customized non-standard tests, for more information please contact us directly or send your test request with order form!
Mechanical destructive tests are carried out mainly for materials and products conformity to requirements or standards and also during expertise for their actual mechanical properties determination.
- Destructive test load between 0.1 kN … 250 kN and temperature -80°C …+ 650°C.
- Slow (quasi-static) and/or cyclic loading (fatigue test).
- Products: fasteners, concrete reinforcing steel, railway rails.
- The most typical properties to be determined are tensile strength, yield strength, elongation at break.
- It is also possible to measure the deformations in 3D using cameras and the Digital Image Correlation – DIC method.
NB! All specimens are prepared according to standards requirements therefore it is essential to consent samples dimensions before testing!
Methods for chemical composition analysis:
- Spectral analysis (Atomic Emission Spectroscopy – AES)
- SEM-EDS – Scanning Electron Microscopy with Energy Dispersive Spectroscopy
Chemical composition is analysed mainly during conformity evalution to determine metals and their alloys actual chemical composition more precisely their chemical elements concentration.
Main Fe-based alloys (steel, cast iron), Cu-based alloys (bronze, brass etc.) and Al-based alloys chemical composition is determined usually with AES method. For smaller specimens it is possible to use induction melting device.
SEM-EDS method is used mostly for material microstructure, coatings or smaller specimens.
Methods for chemical composition analysis:
- Spectral analysis (Atomic Emission Spectroscopy – AES)
- SEM-EDS – Scanning Electron Microscopy with Energy Dispersive Spectroscopy
Chemical composition is analysed mainly during conformity evalution to determine metals and their alloys actual chemical composition more precisely their chemical elements concentration.
Main Fe-based alloys (steel, cast iron), Cu-based alloys (bronze, brass etc.) and Al-based alloys chemical composition is determined usually with AES method. For smaller specimens it is possible to use induction melting device.
SEM-EDS method is used mostly for material microstructure, coatings or smaller specimens.
Microstructure analysis methods:
- Steel grain size EN-ISO 643
- Steel non-metallic inclusions ASTM E45
Macrostructure analysis tests:
- Fracture surface analysis
- Porosity
- Micro/macro cracks
- The purpose of structural analysis of metals and their alloys is to evaluate material conformity to requirements and to assess heat treatment quality. Metals and alloys cleanliness (different inclusions), grain size and microstructure are evaluated.
- The purpose of fracture surface analysis is to identify the nature of fracture – brittle or ductile and root cause of failure for example overload, corrosion etc.
Light optical microscope optical magnification is between 4,7x … 1000x. In case of need, using scanning electron microscopy (SEM) enables using higher magnifications (up to 20.000x).
For microstructure analysis, preparing a cross-section from examined sample is needed. For that, sampled material is encapsulated with mounting with a plastic shell which prepares the sample for the following metallographic grinding, polishing and etching steps. Both, hot and cold mounting are available (cross-section diameter 25 mm … 50 mm).
LOM and/or SEM methods are used for macrostructure and fracture surface analysis.
Microstructure analysis methods:
- Steel grain size EN-ISO 643
- Steel non-metallic inclusions ASTM E45
Macrostructure analysis tests:
- Fracture surface analysis
- Porosity
- Micro/macro cracks
- The purpose of structural analysis of metals and their alloys is to evaluate material conformity to requirements and to assess heat treatment quality. Metals and alloys cleanliness (different inclusions), grain size and microstructure are evaluated.
- The purpose of fracture surface analysis is to identify the nature of fracture – brittle or ductile and root cause of failure for example overload, corrosion etc.
Light optical microscope optical magnification is between 4,7x … 1000x. In case of need, using scanning electron microscopy (SEM) enables using higher magnifications (up to 20.000x).
For microstructure analysis, preparing a cross-section from examined sample is needed. For that, sampled material is encapsulated with mounting with a plastic shell which prepares the sample for the following metallographic grinding, polishing and etching steps. Both, hot and cold mounting are available (cross-section diameter 25 mm … 50 mm).
LOM and/or SEM methods are used for macrostructure and fracture surface analysis.
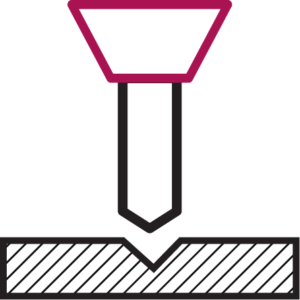
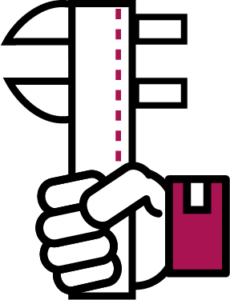
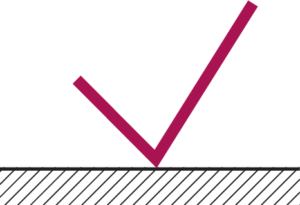
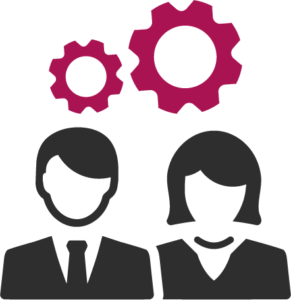
- Hardness testing
- Measurement of components
- Surface roughness measurement
- Expertise and consultations
Hardness measurement methods:
- Brinell hardness EN-ISO 6506-1
- Vickers hardness EN-ISO 6507-1
- Rockwell hardness EN-ISO 6508-1
- Universal hardness (instrumented indentation test) EN-ISO 14577
Measuring material hardness enables to evaluate heat treatment conformity to requrements. For some materials, it is also possible to evaluate material tensile strenght through hardness measurement results.
Brinell hardness is mainly used for determine hardness of soft and medium hardness steels. Vickers hardness is used for welds and Rockwell hardness for tempered steel and aluminum alloys.
- Vickers scale HV 0,01 … HV 30.
- Brinell load 1 kgf … 3000 kgf, ball dimensions 1; 2,5; 5 and 10 mm.
- Rockwell scales HRA, HRB, HRC. Additional loads 15 kgf, 30 kgf and 45 kgf.
For all methods suitable sample shape, thickness and surface finish is required to carry out hardness measurement. For more information please contact us through order form.
Hardness measurement methods:
- Brinell hardness EN-ISO 6506-1
- Vickers hardness EN-ISO 6507-1
- Rockwell hardness EN-ISO 6508-1
- Universal hardness (instrumented indentation test) EN-ISO 14577
Measuring material hardness enables to evaluate heat treatment conformity to requrements. For some materials, it is also possible to evaluate material tensile strenght through hardness measurement results.
Brinell hardness is mainly used for determine hardness of soft and medium hardness steels. Vickers hardness is used for welds and Rockwell hardness for tempered steel and aluminum alloys.
- Vickers scale HV 0,01 … HV 30.
- Brinell load 1 kgf … 3000 kgf, ball dimensions 1; 2,5; 5 and 10 mm.
- Rockwell scales HRA, HRB, HRC. Additional loads 15 kgf, 30 kgf and 45 kgf.
For all methods suitable sample shape, thickness and surface finish is required to carry out hardness measurement. For more information please contact us through order form.
- Automated thermal cutting process capability control
EN 1090-2 - Average surface roughness and perpendicularity tolerance ISO 9013
Products and components geometrical and post-process workpieces control.
Examples of controlled products:
- wire strands;
- reinforcement and prestressed steels;
- thermal cut details.
- Automated thermal cutting process capability control
EN 1090-2 - Average surface roughness and perpendicularity tolerance ISO 9013
Products and components geometrical and post-process workpieces control.
Examples of controlled products:
- wire strands;
- reinforcement and prestressed steels;
- thermal cut details.
- Surface roughness measurement ISO 9013
Surface roughness measurements. Measurements are performed by contact profilometer, enabling main outputs as Ra, Rz, Rmax, Rp, Rv etc.
- Surface roughness measurement ISO 9013
Surface roughness measurements. Measurements are performed by contact profilometer, enabling main outputs as Ra, Rz, Rmax, Rp, Rv etc.
We offer a professional expertise work because we are used to the high demands of companies and have understanding of several production processes.
We also offer consultations and can assist in improving the production process and performing quality control of production. We have long-term experience of cooperation with industrial companies
Expertise is mostly used in finding out the reasons for the breakage or failure of parts or the processes. Expertise is not only performed to resolve disagreements between the parties, but also in situations where the manufacturer or the user of the product examines some product-related process or product characteristic:
- causes of breakage/wear of one particular part;
- fast machine part, etc., which occurred as a result of repair or reconstruction;
- breakage/wear; causes of scrap parts in production;
- the suitability/properties of the material used or applied.
When ordering expertise, the following circumstances must be taken into account:
- the expertise is performed on a specific material/detail brought by the customer;
- studies and opinions performed in expert examination must remain within the competence of the laboratory;
- it is not possible to answer all questions unambiguously.
For more informaton, please contact us thorugh order form!
We offer a professional expertise work because we are used to the high demands of companies and have understanding of several production processes.
We also offer consultations and can assist in improving the production process and performing quality control of production. We have long-term experience of cooperation with industrial companies.
Expertise is mostly used in finding out the reasons for the breakage or failure of parts or the processes. Expertise is not only performed to resolve disagreements between the parties, but also in situations where the manufacturer or the user of the product examines some product-related process or product characteristic:
- causes of breakage/wear of one particular part;
- fast machine part, etc., which occurred as a result of repair or reconstruction;
- breakage/wear; causes of scrap parts in production;
- the suitability/properties of the material used or applied.
When ordering expertise, the following circumstances must be taken into account:
- the expertise is performed on a specific material/detail brought by the customer;
- studies and opinions performed in expert examination must remain within the competence of the laboratory;
- it is not possible to answer all questions unambiguously.
For more informaton, please contact us thorugh order form!